Blog
Inventory and Spare Parts Planning & Optimization in the Age of AI & IoT
Unless you work in supply chain, you might be shocked to learn about the degree of inefficiency and waste in the world due to poor inventory management. No wonder it’s usually kept under wraps—or becomes controversial when exposed, as happened during the early days of Covid vaccine distribution when significant spoilage and waste occurred despite overwhelming demand.
Inventory challenges are not exclusive to perishable goods. Tires, for instance, can develop flat spots, dry rot, or lose their elasticity if stored for extended periods without proper care. Electronic Components like circuit boards and chips can likewise oxidize or degrade over time.
And then there’s the issue of obsolescence, which is especially common for electronics, apparel, appliances and automotive parts.
Given these challenges, whether you’re overseeing equipment spare parts, materials for manufacturing, or inventory for your distribution business, advanced inventory management strategies are more applicable and needed now than ever. Thanks to recent advances in data and AI technologies, such as RFID-based inventory tracking, AI-powered prediction and forecasting techniques, and advanced optimization algorithms, these strategies can now be implemented much more quickly and cost-effectively.
In this 6-part post, we’ll explore five essential aspects of inventory optimization: Demand Forecasting, Strategic Planning, Tactical Inventory Optimization, Inventory Replenishment Planning, and Inventory Logistics & Order Fulfillment, along with some of the AI-related technologies that enable these use cases.
1. Demand Planning & Forecasting: Anticipating Needs
Most organizations know that their demand forecasting for parts/materials and finished goods could be better. In many cases, the forecast for next year/week/month is simply the prior period’s actual with an adjustment factor applied. In many cases, such as new product introductions (NPIs) without historical sales data, forecasting is more of an art than a science.
Fortunately, machine learning techniques now offer better forecasting capabilities. For example, clustering techniques can forecast new items by analyzing similar products with historical data. Spare parts demand, meanwhile, hinges on historical repair data and preventative maintenance plans and schedules.
A growing number of organizations are now using advanced statistical methods and machine learning algorithms to “refine their art” and help predict future demand (and maintenance) with greater accuracy. By analyzing historical data, market trends, and external factors such as seasonality and economic indicators, organizations in all industries are finding that they can, indeed, create better forecasts.
With the proper integrations with your ERP and other systems that house your data, modern forecasting systems can keep the forecasts updated, reacting to market shifts in near-real time, thus giving an edge over the competition.
For example, a company using advanced forecasting tools might notice a surge in demand for certain products due to a trending social media topic – Large Language Models (LLMs) can be used for this. Weekly or daily forecast systems can then incorporate the new signal and automatically propose an adjustment to the forecast. This proposal could be automatically flagged for review by the planner who can test out the impact of adjusting the production schedules or inventory levels before committing the decision to make any adjustment.
Before embarking on any forecasting improvement project, it’s important to be sure that any improvements in forecasting accuracy can actually be effectively utilized. That means you need systems and processes in place to be able to incorporate these improvements into your operations.
2. Strategic Inventory Planning: The Right Stock at the Right Place
Once you have a solid forecast, the next step is strategic planning. This involves determining where and how much of each part, material, or item should be stocked. This sounds simple but can get very complex because of the many factors that need to be considered simultaneously.
Consider the problem airlines face with spare parts management. Critical parts and components must be readily available to prevent costly flight delays. However, it is not feasible or cost-effective to stock every item at every location. Questions arise: How critical is each item? What is the supplier’s lead time versus what is acceptable? Can centralized stocking locations efficiently serve multiple airports? And how soon might the parts become obsolete?
Although this post is focused on using AI, problems like this will continue to warrant strategic planning sessions with business stakeholders to make these decisions effectively and on an ongoing basis. By bringing together stakeholders from different parts of the business, these sessions enable comprehensive consideration of varied perspectives and requirements, leading to more informed and balanced strategic decisions. Nevertheless, AI-powered planning and scenario analysis tools effectively support these strategic meetings by providing objective, data-driven insights.
Advanced planning tools and algorithms enable the simultaneous evaluation of factors such as demand patterns, supplier reliability, lead times, transportation costs, and service level requirements. This comprehensive analysis, often referred to as Multi-Echelon Inventory Optimization (when conducted across multiple locations in the supply chain from central warehouses to regional distribution centers to individual retail outlets), helps balance the need for high service levels with the goal of minimizing inventory carrying costs.
3. Tactical Inventory Management: Planning with More Precision
Once the strategic design of your network is in place and you have a general idea of where inventory should be located, you will want to get more granular and regularly fine-tune the plan. This means shifting to a more short-term focus, like weekly – so that you can align with the most current forecast. Therefore, for tactical inventory optimization, your planning horizon typically ranges from 3 to 18 months.
The goal here is the same as in strategic planning – to maintain the right inventory levels at the individual SKU level and in a way that balances holding costs, ordering costs, and stockout costs. But what’s different is that it involves setting precise reorder points (ROP) and order quantities (EOQ or Economic Order Quantities) by SKU in a way that minimizes costs while still meeting service level objectives.
A crucial component of this process is determining the appropriate level of safety stock. Safety stock acts as a buffer against uncertainties in demand and supply. The amount of safety stock needed is influenced by several factors, including:
- Forecast Accuracy: How reliable are your demand forecasts? The less accurate your forecast, the more safety stock you might need.
- Supplier Reliability: Do your suppliers consistently deliver on time? Variability in supplier performance can necessitate higher safety stock.
- Replenishment Lead Times: Is your replenishment source nearby or an ocean away? Longer lead times generally require more safety stock to mitigate the risk of stockouts.
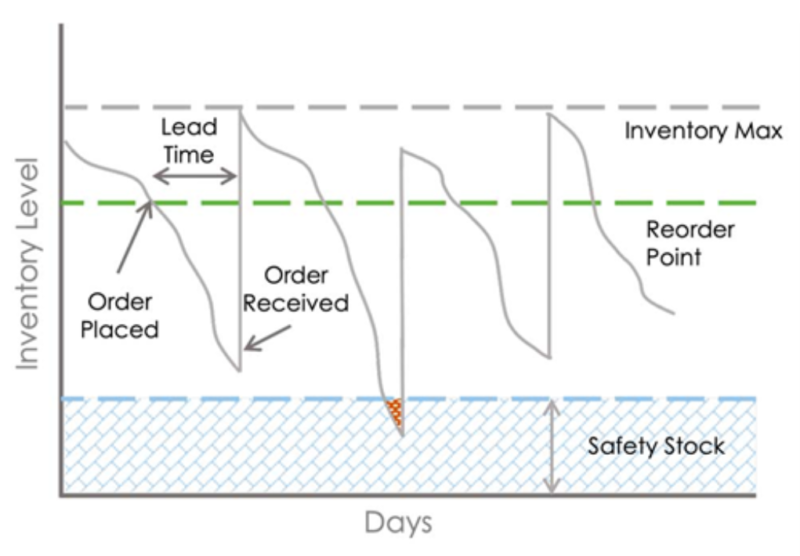
The key here, as in all inventory and spare parts planning applications, is to be as dynamic as possible so that the inventory is adjusted and therefore continually optimized based on real-time data and demand variability.
4. Logistics & Order Planning: Delivering Excellence
The next piece of the puzzle is logistics and order planning. This covers a broad range of strategies from improving the movement of items from receiving to delivery to customer or manufacturing line. This can include building detailed daily or weekly order schedules and logistics plans to address delivery mode selection, carrier choice, truckload optimization, efficient routing, and even packaging considerations. The primary objective is to ensure the timely and cost-effective delivery of goods while exceeding customer expectations.
Advanced optimization methods often play a big role in this domain, empowering businesses to maximize transportation asset utilization, minimize costs, and streamline operations across the supply chain.
Examples of Optimization Use Cases:
- Transport Mode Selection: Decision-making involves choosing the most suitable transport mode (air, sea, rail, road) based on factors like shipment urgency, cost-efficiency, and environmental impact.
- Carrier Selection and Routing Optimization: Optimal selection of carriers and routes using algorithms that consider factors such as delivery times, costs, and service levels, ensuring efficient distribution.
- Packaging Optimization: Evaluating packaging constraints and considerations such as Economic Order Quantity (EOQ) versus container capacity to determine optimal lot sizes. This may include re-evaluating packaging strategies to improve manufacturing flow and alleviate bottlenecks.
- Warehouse Management and Slotting Optimization: Enhancing warehouse efficiency through advanced slotting algorithms that optimize product placement based on picking patterns, product velocities, and storage constraints. This optimization reduces travel time, minimizes handling costs, and increases throughput by strategically locating high-demand items.
- Just-in-Sequence and Just-in-Time (JIS/JIT) Delivery: Implementing intelligent logistics systems to synchronize part deliveries with manufacturing schedules, minimizing inventory buildup on the factory floor and ensuring seamless production flow.
Case Example
An automotive manufacturer partnered with DecisionBrain to implement a custom inbound logistics planning system. The system optimized monthly truck routes for parts delivery to assembly plants, employing JIS and JIT methods to align part delivery with assembly line requirements. Through 3-D truck load optimization and smart “milk runs,” the manufacturer reduced monthly planning time from 2.5 person-days to just one hour, significantly improving operational efficiency and cost-effectiveness.
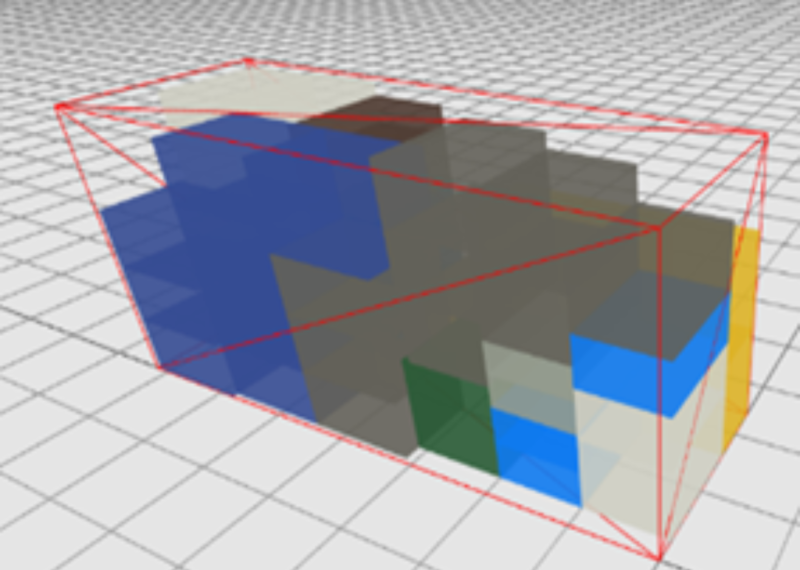
In summary, logistics optimization encompasses a wide range of strategies and technologies aimed at enhancing the movement of goods throughout the supply chain. By leveraging advanced algorithms and data-driven insights, businesses can achieve operational excellence, reduce costs, and deliver superior customer experiences.
5. Operational Execution: Inventory Replenishment & Logistics Planning
Inventory replenishment and operational execution activities are continuous processes that are executed on the most frequent basis, typically daily or weekly, to maintain optimal inventory levels and ensure a smooth flow of goods through the supply chain. It involves detailed planning to determine when, where, and how much to reorder for each SKU, taking into account granular demand forecasts, supplier lead times, and current inventory levels.
Advanced algorithms and AI play a crucial role here in optimizing replenishment plans by analyzing historical data and real-time inventory levels as discussed in the prior section, but also supplier performance. This is especially important when dealing with volatile markets subject to frequent demand shifts and/or supply chain disruptions, like the sort that caused our glass beverage bottle supplier earlier to run into issues.
Effective replenishment also involves close collaboration with suppliers to synchronize activities, enhance responsiveness, and reduce lead times.
Automated replenishment systems, driven by AI and machine learning, use real-time data to trigger orders automatically. These systems continuously adjust reorder points and quantities based on current demand patterns, ensuring optimal inventory levels with minimal manual intervention. For example, a retailer using an automated system integrated with POS data can maintain availability of fast-selling items while managing slow-moving stock efficiently.
Emerging Innovations in Supply Chain and Inventory Management
As the landscape of inventory and supply chain management evolves, several cutting-edge techniques are emerging that promise to push the boundaries of what is possible. These advanced methods leverage the latest in artificial intelligence, machine learning, and data analytics to create unprecedented levels of efficiency and accuracy.
Reinforcement Learning for Order Planning and Execution
Reinforcement learning (RL) is an area of machine learning where an agent learns to make decisions by performing actions and receiving feedback from those actions. In supply chain management, RL can be applied to optimize order planning and execution. For instance, an RL-based system can dynamically adjust order quantities and timings based on real-time data, historical patterns, and supply chain disruptions. By continuously learning and improving from the feedback received, these systems can achieve optimal inventory levels while minimizing costs and enhancing service levels.
Large Language Models (LLMs) in Supply Chain Management
There is a growing interest in applying LLMs like GPT-4 to supply chain and inventory optimization. On the demand planning side, as already mentioned, LLMs can analyze vast amounts of textual data, such as news articles, social media posts, and market research to identify trends and predict disruptions.
Beyond demand forecasting, LLMs have the potential to enhance the accessibility and value of optimization-based planning systems. For instance, an optimization-powered inventory planning system might offer a chat-like interface for users to ask questions about ways in which to achieve specific KPI objectives – perhaps by relaxing certain business constraints. This would eliminate the need for manually running and comparing various what-if scenarios, streamlining the decision-making process.
On the procurement side, LLMs can analyze supplier payment terms and delivery histories to negotiate better terms or suggest alternative suppliers. Generative AI models are also being applied to contract negotiation, drafting and invoicing.
Digital Twins for Real-Time Simulation and Optimization
Digital twins are virtual replicas of physical assets, systems, or processes that enable organizations to simulate real-world scenarios in a risk-free environment. In supply chain management, digital twins serve an important role in modeling and optimizing not just inventory but the entire supply chain network.
Optimization-powered systems, which combine machine learning forecasting methods with mathematical optimization models embedded into scenario-based applications, are one approach to digital twins. These systems allow for scenario testing, comparison of Key Performance Indicators (KPIs), and the simulation of different strategies. By leveraging real-time data feeds such as incoming shipment schedules, vehicle locations, and inventory levels, optimization-powered digital twins ensure forecasts remain updated and provide insights into potential bottlenecks. They enhance overall supply chain efficiency by dynamically adjusting operations based on current conditions and predictive analytics.
In addition to optimization-powered systems, other types of simulation systems exist in supply chain management. These true “simulation systems” utilize different approaches, such as discrete event simulation (DES) or agent-based modeling (ABM). DES simulates the operation of complex systems as discrete events over time, allowing for the analysis of process flows, resource utilization, and system performance under various conditions. ABM, on the other hand, models individual entities (agents) and their interactions within a system, providing insights into emergent behaviors and decision-making processes.
Both optimization-powered digital twins and traditional simulation systems contribute to strategic decision-making by enabling organizations to experiment with different scenarios, identify potential risks, and optimize resource allocation and operational workflows. These tools are invaluable in driving continuous improvement and resilience across supply chain operations, ensuring adaptability in dynamic market environments.
Blockchain for Enhanced Transparency and Security
While not strictly speaking an “AI” technology, blockchain is still a relatively new and very promising “AI-adjacent” technology for addressing one of the biggest supply chain challenges today, which is transparency, traceability and security. Yet its adoption has been slower than anticipated.
The promise of blockchain is that it would serve as an immutable, decentralized ledger so that every transaction and movement of an item within the supply chain would be securely recorded and verifiable, similar to the way ownership of real estate properties is recorded in public land registries, but for products traversing global supply networks. This holds significant potential to address widespread fraud and improve traceability and compliance with regulatory standards.
For example in the pharmaceutical industry, blockchain can improve supply chain integrity by enabling the tracking of drugs from manufacturing through distribution. This could prevent counterfeit products from entering the market and enhance consumer safety. Similarly, in automotive and electronics sectors, where component authenticity and supply chain visibility are critical (think solar panels, batteries, communication chips, etc), blockchain can provide a trusted record of provenance as well as maintenance history.
The reasons for the slow adoption of blockchain are varied and include things like complexity of aligning multiple stakeholders’ systems, technology interoperability and scalability issues. Moreover, concerns about data privacy, regulatory compliance, and the high initial costs associated with implementation remain significant barriers to adoption.
Ready to transform your inventory management?
Contact DecisionBrain today to discover how our solutions can help your business thrive.
DecisionBrain is a leading provider of advanced decision support software that is used to solve the world’s hardest supply chain, workforce and maintenance planning, scheduling & logistics optimization problems. With over 400 person-years of experience in machine learning, operations research and mathematical optimization, DecisionBrain delivers custom-fit decision support systems where packaged applications fall short. Read more about us or contact us to talk about our solutions!
About the Author
Justin brings over 20 years of experience in analytics, supply chain management, professional services, and manufacturing operations to DecisionBrain. His career has centered using data and analytics to improve operations. He has held leadership positions at Accenture, Caterpillar, Opex Analytics, and Coupa Software (Llamasoft). Justin has a BSc in Engineering Mechanics from the University of Illinois and a MSc in Analytics from the University of Chicago.
About the Author
Nevra brings over 20 years of enterprise software sales, marketing and leadership experience to DecisionBrain. Nevra has devoted her career to helping organizations apply big data, analytics, optimization and other artificial intelligence technologies to make better decisions. Before DecisionBrain, Nevra helped grow sales at several early-stage companies such as Databricks, Syncsort (now Precisely), RedPrairie (now BlueYonder), KXEN (now SAP), and ILOG (now IBM). Nevra holds a B.S. in Physics from the University of California, Santa Cruz.