Blog
Dimensionnement des Lots : Défis Réels et Perspectives d’Experts
Le dimensionnement des lots, parfois appelé lot-sizing, est principalement associé aux cas d’utilisation en fabrication et en planification de la Supply Chain tels que la planification des ressources matérielles (MRP) et la planification de la production. Cependant, pour les chercheurs et les ingénieurs spécialistes de l’optimisation mathématique, les problèmes de dimensionnement des lots peuvent se retrouver dans plein de contextes, par exemple :
- Planification et ordonnancement de la production : déterminer les tailles de lots de production.
- Planification des stocks de la chaîne logistique: comment regrouper et positionner les stocks dans les magasins et entrepôts.
- Planification logistique tactique : quand (par exemple, par semaine) déplacer quels lots de produits de l’usine à l’entrepôt.
- Planification de la maintenance : regrouper intelligemment les activités de maintenance.
- Campagnes de marketing : décider de la répartition du budget marketing à allouer entre différents canaux (salons, publicité, réseaux sociaux, etc.).
- Trading de devise : déterminer les meilleures quantités (lots) de devises à échanger en fonction des risques et du rendement.
Dans cet article, nous explorons ce sujet à travers des exemples concrets et des perspectives proposés par Sébastien Beraudy, docteur en recherche opérationnelle et employé chez DecisionBrain.
L’Usine de Jus : un équilibre entre périssabilité et rendements
Imaginez que vous dirigez une usine qui produit divers jus de fruits. Vous disposez de plusieurs fruits comme des pommes et des fraises, chacun avec des coûts et des profils de demande différents. Les fraises sont plus chères mais très populaires, tandis que les pommes sont moins coûteuses mais moins demandées. Votre objectif est de produire les bons mélanges de jus pour répondre à la demande des clients sans gaspiller de fruits ni générer des coûts inutiles.
Dans ce scénario, vous ne pouvez produire que quatre types de jus : du pur jus de pomme, du pur jus de fraise, un mélange avec 5 % de fraise et 95 % de pomme, et un mélange premium avec 20 % de fraise. Le dimensionnement des lots implique de déterminer la quantité optimale de chaque type de jus à produire pour chaque période. Il est nécessaire de trouver un équilibre entre les coûts, la satisfaction de la demande et la minimisation des pertes de produits. Si vous produisez trop de mélange premium, il risque de se périmer avant d’être vendu. Si vous en produisez trop peu, vous risquez de manquer des ventes et de décevoir les clients.
Sébastien explique ainsi : « Le dimensionnement des lots est semblable à un puzzle complexe où toutes les pièces doivent s’emboîter parfaitement. Il faut prendre en compte de nombreux aspects, tels que les coûts de production, les limites de stockage, la péremption des différents ingrédients, etc. C’est un problème difficile, mais bien le résoudre peut conduire à des économies de coûts importantes et à des gains d’efficacité. »
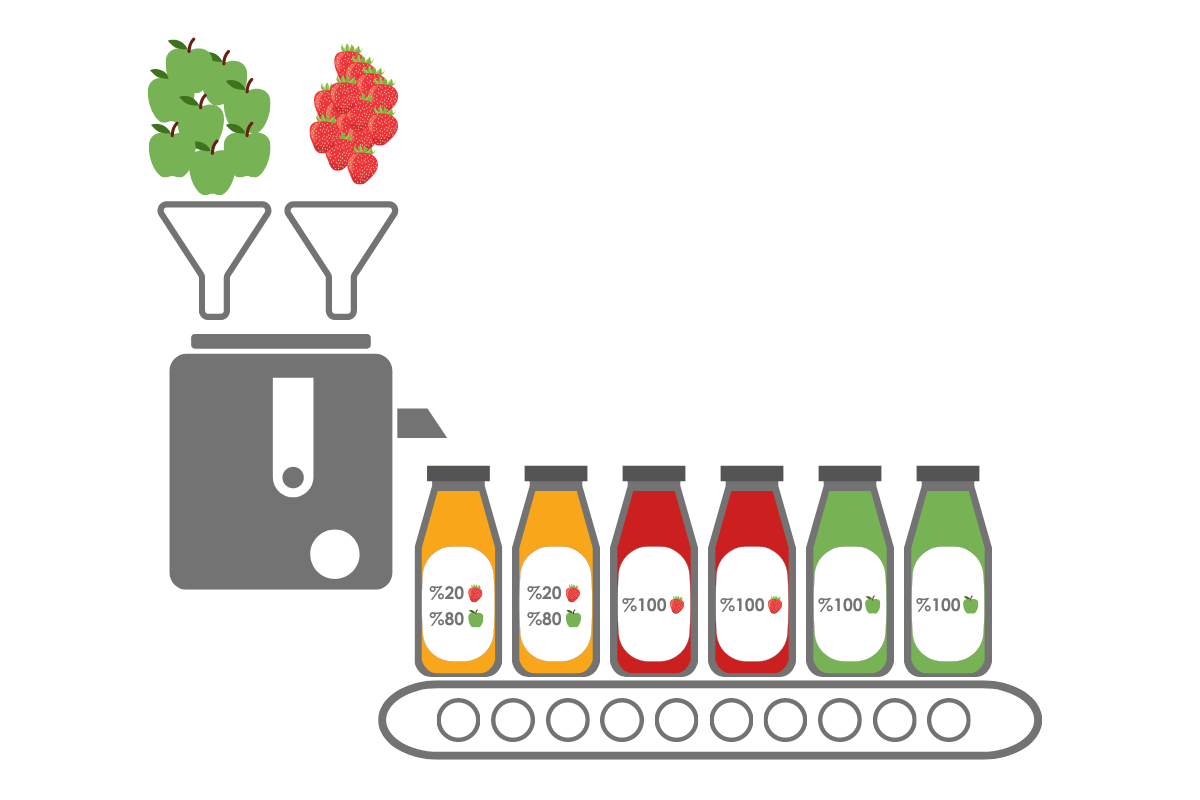
L’exemple de l’Autoroute : Prioriser les Commandes Prioritaires
Examinons maintenant un autre type de problème de dimensionnement des lots. Imaginez une autoroute très fréquentée avec des voitures circulant à vitesse constante. Arrive une ambulance en intervention. Toutes les voitures doivent alors ajuster leur vitesse pour la laisser passer. On peut comparer ce cas à une ligne de production qui doit soudainement prioriser une commande de haute importance.
Dans l’industrie, vous pouvez avoir un plan de production régulier, mais de temps à autre, une commande prioritaire arrive et doit être traitée en urgence. Cela signifie réorganiser votre plan de production pour intégrer cette commande urgente sans perturber excessivement le flux des autres productions. Si vous ne modélisez pas correctement les différents délais de production, cela peut aboutir à un plan totalement inutilisable. On peut comparer cela à des voitures sur l’autoroute qui ne verraient pas à temps l’alerte d’un accident sur leur GPS : elles pourraient rater l’opportunité de sortir avant les bouchons ou manquer celle de réintégrer la route une fois l’accident passé, arrivant à destination avec plus de retard que nécessaire.
Sébastien compare cela à la gestion des délais dans le dimensionnement des lots. « Les délais peuvent être imprévisibles et variables, comme le trafic sur une autoroute. Calculer la moyenne des délais peut sembler être une solution simple, mais cela ne tient pas compte des variations et des retards imprévus – comme lors de travaux routiers, similaires à une station de production en panne ou un approvisionnement qui n’arrive pas à temps. Si vous ne modélisez pas ces variations avec précision, vous risquez d’avoir un plan tout simplement inapplicable en pratique, ce qui pourrait perturber l’ensemble de la chaîne de production ! »
Pourquoi les Problèmes de Dimensionnement des Lots sont Complexes – L’Exemple des Délais de production
L’exemple des délais de production est un sujet intéressant pour les universitaires et les professionnels de l’industrie car il illustre comment l’ajout d’une seule contrainte peut affecter drastiquement la résolution des problèmes de dimensionnement des lots. Ce qui va directement influencer la capacité du logiciel à générer des plans de production efficaces.
Tout d’abord, examinons comment le dimensionnement des lots s’applique en production. Changer de produit sur la ligne de production va nécessiter une opération d’ajustement (par exemple, le nettoyage nécessaire pour passer de la peinture rouge à la peinture blanche), ce qui réduit l’efficacité. Cela incite à rassembler la production d’un même produit en des lots de grande taille. Cependant, cela se traduit aussi par des niveaux de stocks élevés (qui mènent aux problématiques abordées dans notre article sur l’optimisation des stocks) et potentiellement des problèmes de satisfaction lorsque la demande varie. Il faut donc trouver un équilibre en optimisant les tailles des lots pour fournir un bon taux service des lignes de production, tout en minimisant les coûts de stockage.
Cependant, lors de la planification, le temps de changement de produit — qui peut comprendre le temps nécessaire à la réception de la peinture blanche du fournisseur, le temps de nettoyage, de la préparation avant d’appliquer la peinture, en passant par le temps de séchage — doit être spécifié avec précision et pris en compte par le système d’optimisation. C’est plus facile à dire qu’à faire. Voici pourquoi :
- Variabilité : Les délais de production/livraison peuvent être très variables et imprévisibles en raison de facteurs tels que la fiabilité des fournisseurs, les retards de transport et les problèmes de production. Considérer seulement la moyenne du délai simplifie trop cette variabilité, ce qui entraîne des imprécisions dans la planification.
- Interactions complexes : Les délais de production interagissent avec d’autres contraintes (par exemple, la capacité de production, les limites de stockage) de manière complexe. Un retard dans une partie de la chaîne logistique peut avoir un effet domino sur le reste de la chaîne, ce qui complique le processus d’optimisation.
- Nature Dynamique : Les délais peuvent évoluer avec le temps en raison de conditions du marché, de changements de fournisseurs ou d’améliorations des processus internes (par exemple, opter pour une peinture plus écologique peut augmenter le temps de séchage). Les modèles statiques qui utilisent des estimations en moyenne des délais n’arrivent pas à s’adapter à ces changements.
- Non-linéarité : Les délais de production ne croissent pas toujours de manière linéaire avec la charge. Par exemple, plus vous produisez, plus le délai par unité peut être long, mais pas de manière simple et prévisible. Pour gérer cela, une approche consiste à analyser les données du passé pour regarder les variations des délais en fonction de la charge, puis à décomposer cette courbe en morceaux plus petits et quasiment linéaires pouvant être intégrés dans la planification. Une autre approche consiste à utiliser des simulations pour voir comment les différents plans de production affectent les délais, puis à ajuster le plan en conséquence. Cette complexité rend le problème plus difficile à résoudre avec des méthodes simples.
De nombreuses autres contraintes, telles que les capacités de production, les limites de durée de vie ou la disponibilité des ressources, peuvent également complexifier le problème et nécessiter des approches sophistiquées pour être traitées efficacement.
Dimensionnement des Lots d’Achat : Équilibrer Prix d’achat et Gestion des Stocks
Le dimensionnement des lots d’approvisionnement est un autre cas d’application fréquent. Il s’agit d’optimiser les quantités d’achat pour équilibrer les économies d’échelles sur les prix et la gestion des stocks. Les achats en gros offrent des coûts unitaires plus bas, mais cela signifie également des coûts de stockage accrus, ce qui peut ne pas être pertinent pour des articles à la demande incertaine ou à durée de vie courte. Des facteurs comme les coûts d’emballage et de transport peuvent également devoir être pris en compte. Un outil de planification efficace doit intégrer tous ces coûts ainsi que les divers objectifs commerciaux pour proposer les bonnes tailles de lots d’approvisionnement. Il est également essentiel de mettre à jour dynamiquement les tailles de lots afin qu’elles restent en adéquation avec les évolutions de la demande et des conditions d’approvisionnement.
Conclusion & Ressource pour aller plus loin
Le dimensionnement des lots est un aspect crucial de nombreux problèmes de planification et de scheduling dans toute la chaîne logistique. Que vous gériez des stocks, optimisiez des processus de fabrication ou rationalisiez des stratégies d’achat, dimensionner correctement vos opérations est d’une importance capitale.
Bien que de nombreuses applications logicielles gèrent le dimensionnement des lots dans une certaine mesure, l’ajout d’une nouvelle contrainte peut complexifier considérablement le problème. C’est pourquoi il est utile de consulter des experts en supply-chain et en recherche opérationnelle pour évaluer la faisabilité de votre usage spécifique.
Relever ces défis nécessite une expertise et des solutions innovantes. Chez DecisionBrain, notre équipe, qui comprend des experts comme Sébastien, s’engage à développer des stratégies efficaces et efficientes pour aider les entreprises à prospérer dans l’environnement concurrentiel d’aujourd’hui. Comprendre et aborder les complexités du dimensionnement des lots peut conduire à des avantages considérables, rendant cet effort tout à fait rentable.
Pour un approfondissement des aspects techniques du dimensionnement des lots et de la variabilité des délais de production, vous pouvez consulter la thèse de Sébastien ici.
Vous êtes confronté à des problématiques de dimensionnement des lots dans vos opérations ?
Notre équipe d’experts chez DecisionBrain est là pour vous aider.
DecisionBrain est un fournisseur de premier plan de logiciels avancés d’aide à la décision utilisés pour résoudre les problèmes d’optimisation de la supply chain, de la planification de la main-d’œuvre et de la maintenance, de l’ordonnancement et de la logistique les plus difficiles au monde. Avec des années d’expérience dans l’apprentissage automatique, la recherche opérationnelle et l’optimisation mathématique, DecisionBrain fournit des systèmes d’aide à la décision sur mesure là où les applications packagées ne suffisent pas. Contactez-nous pour en savoir plus sur nous et nos solutions !